Pumpspeicherkraftwerk Limberg 3: 355 Tonnen Rotor erfolgreich eingehoben
Die Großbaustelle des Pumpspeicherkraftwerks Limberg 3 im Salzburger Kaprun erreichte am 12. September einen weiteren Meilenstein ihrer Projektumsetzung: Der Rotor von Maschine 1 wurde erfolgreich installiert. Dazu musste das 355 Tonnen schwere Stahlteil mit dem für diesen Zweck ausgerichteten Deckenkran in den Stator eingehoben werden. Für den strategischen Zeitplan des Projektbetreibers VERBUND bedeutet dies einen großen Fortschritt im Hinblick auf Montage und Endfertigung. Ziel des ehrgeizigen Zeitplanes ist es, bis 2025 in Betrieb zu gehen.
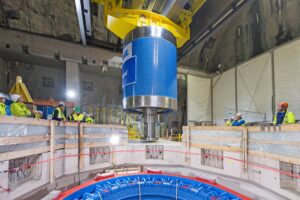
© VERBUND / Johannes Wiedl
Der Rotor in seiner Gesamtheit ist mit einer Masse von 355 Tonnen das schwerste Maschinenteil, das auf der Baustelle Limberg 3 bewegt werden muss. Aufgrund seiner enormen Abmessungen und seines Gewichts muss dieser in der Kaverne gefertigt werden. Die Höhe der Kaverne von 17 Metern wurde aus diesem Grund auf die dafür erforderlichen Kipp- und Hebevorgänge hin optimiert. Der gesamte Prozess von der Fertigung bis zur Installation ist langwierig und erfordert von allen Beteiligten viel Geduld. Fast ein Jahr wurde an der Fertigung und dem Zusammenbau des Rotors im Berg gearbeitet. Umso wichtiger, dass am Tag X das Zusammenspiel zwischen Kranfahrer und Einweiser zu 100% funktioniert. Und das tat es. Der gigantische Stahlkoloss wurde mit nur 4 bis 5 Millimeter Spielraum mit den Hallenkränen in den Stator eingehoben. Fingerspitzengefühl, Nervenstärke und gute Abstimmung des Personals sind dabei entscheidend. Nur ein kleiner Fehler oder Schwingungen könnten den Stator schwer beschädigen. Umso größer war die Freude des gesamten Projektteams, dass der schwierigste und schwerste Hub des gesamten Projekts reibungslos ablief und nach drei Stunden erfolgreich abgeschlossen werden konnte.
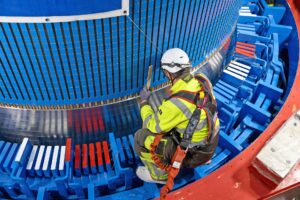
© VERBUND / Johannes Wiedl
Wichtiger Faktor für Energiewende
Limberg 3 stellt eine Erweiterung der Glockner-Kaprun-Kraftwerksgruppe im Herzen der österreichischen Alpen dar und gilt als das modernste Pumpspeicherkraftwerk Österreichs. Wie schon zuvor Limberg 2 wird das neue Limberg 3-Kraftwerk vollständig unterirdisch zwischen den beiden bestehenden Speicherseen — Mooserboden und Wasserfallboden — als weiteres kavernengestütztes Speicherkraftwerk errichtet. Um zusätzliche Speicherkapazität und Flexibilität zu erreichen, wird der Damm des bestehenden Wasserfallboden-Stausees um weitere 8 m erhöht. Mit einer Gesamtkapazität von 480 MW sowohl im Turbinen- als auch im Pumpbetrieb ist Limberg 3 als modernes, flexibles und leistungsstarkes Pumpspeicherkraftwerk konzipiert. Diese Leistungskapazität entspricht dabei der Energieerzeugung von etwa 60 großen Windkraftanlagen. Nach seiner Fertigstellung wird das Kraftwerk extrem flexibel auf den Bedarf an Ausgleichs- und Regelenergie im Netz reagieren und somit den Anforderungen der aktuellen Energiewende und den damit verbundenen Anforderungen an die Netzstabilität gerecht werden können. Mit dem kompletten Engineering, der Lieferung, Montage und Inbetriebnahme des technischen Herzstücks dieser komplexen leistungsstarken Anlage wurde der international agierende Wasserkraftspezialist ANDRITZ beauftragt, der die zwei drehzahlvariablen asynchronen Motorgeneratoren (DFIM) inklusive Hilfsausrüstung und der beiden AC-Erregereinrichtungen liefert.
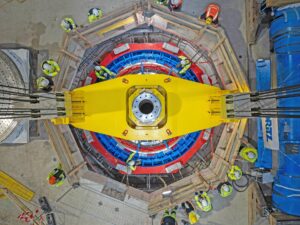
© VERBUND / Johannes Wiedl
Variable Rotordrehzahl essentiell
Im Gegensatz zu Synchronmaschinen, bei denen die Erregung mit Gleichstrom erfolgt, wird bei DFIM-Systemen der Rotor mittels eines Frequenzumrichters mit einem niederfrequenten, dreiphasigen Wechselstrom versorgt. Durch die Steuerung dieser Frequenz ist es möglich, eine variable Rotordrehzahl im Bereich von 450 bis 550 U/min zu nutzen. Diese Fähigkeit kann nicht nur zur Regelung der Blindleistung, sondern auch zur Steuerung der Wirkleistung im Pump- und Turbinenbetrieb verwendet werden. DFIM-Systeme ermöglichen somit höhere Gesamteffizienzen der Anlage und einen sicheren Betrieb der Turbine sowie die Anpassung des Stromverbrauchs an unterschiedliche Betriebsbedingungen. Das Design des Rotors in einer DFIM unterscheidet sich erheblich von dem eines Synchronmotor-Generators und stellt die zentrale Herausforderung für das Design dieses Maschinentyps dar. Als Grundgerüst für den Rotor dient die Rippenwelle mit dem laminierten Rotorblechkern, in den eine dreiphasige Hochspannungswicklung eingesetzt ist. Auf beide Rotorenden werden hochfeste Ringe aufgeschrumpft, die als Halte- und Stützsystem für den Rotorwicklungskopf dienen. Dieser kompakte und effiziente Ansatz des Rotorwicklungskopfes ist eine patentierte ANDRITZ-Konstruktion, die bereits erfolgreich in den Referenzanlagen Goldisthal in Deutschland und Fengning II in China umgesetzt wurde.
Schicht um Schicht zum fertigen Rotor
Bei der Generatorrippenwelle, die auch als „Rohling“ des rotierenden Teils des Motorgenerators bezeichnet wird, handelt es sich um eine zehn Meter lange Schmiedewelle mit aufgeschweißten Stahlrippen, die bereits im Oktober 2023 per Spezialtransporter zur Baustelle in den Berg transportiert und anschließend rückwärts bergauf in die Kraftwerkskaverne gefahren wurde. Dabei wurden nicht weniger als 5,5 Kilometer durch Tunnel zurückgelegt. Danach wurde die Generatorwelle mit einer speziell dafür konstruierten und angefertigten Kipp- und Hebevorrichtung mithilfe von zwei Hallenkränen millimetergenau aufgerichtet und am Rotor-Montageplatz positioniert.
Auf diese Rippenwelle wird im Zuge der Vor-Ort-Fertigung das sogenannte „Rotorblechpaket“ aus unzähligen 0,5 mm dicken Dynamoblechen überlappt geschichtet. Nach mehrmaligen Zwischenpressungen und kontinuierlicher Qualitätsüberwachung wird das Blechpaket abschließend auf 150°C erhitzt, um eine Voralterung bzw. einen Setzvorgang zu erreichen. Nach der finalen Pressung zusammen mit den beidseitigen Endplatten wird das fertige Blechpaket auf die Rippenwelle geschrumpft. Dabei wird das Blechpaket auf bis zu 180°C erwärmt, somit radial aufgeweitet und über Schrumpfleisten auf die Rippenwelle fixiert. Nach diesem Vorgang werden die Wicklungsstäbe in die Rotornuten eingebaut und miteinander hart verlötet. Abschließend werden die beiden äußeren Kappenringe, welche die beiden axialen Enden der Rotorwicklung abstützen, montiert bzw. aufgeschrumpft. Nach genauen elektrischen Prüfungen ist der Rotor dann bereit zum Einheben.
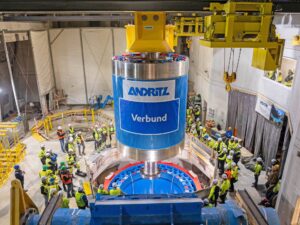
© VERBUND / Johannes Wiedl
Inbetriebnahme 2025
Durch die erfolgte Laminierung mit dem Rotorblechkern erreicht der Rotor seine finalen Ausmaße und sein Gewicht. Mit einer Masse von rund 355 Tonnen entspricht er dem schwersten Einzelhub der gesamten Baustelle. Für ein erfolgreiches Handling mit dem Koloss mussten dementsprechend auch die Hallenkrane ausgelegt sein. Das enorme Eigengewicht bedeutet aber auch, dass die Welle entsprechend robust gebaut sein muss, um den gigantischen Belastungen im Betrieb standhalten zu können. Schließlich ist die Maschine mit atemberaubenden 450 bis 550 Umdrehungen pro Minute schneller als jedes Rennauto. Das muss auch genauso sein, denn das Pumpspeicherkraftwerk soll nicht nur überschüssigen Strom für den Winter speichern, sondern bei Netzschwankungen in Sekundenschnelle zum Ausgleich von Spannungsschwankungen einspringen. Limberg 3 wird dank der beiden drehzahlvariablen Asynchronmotor-Generatoren ein extrem flexibles Pumpspeicherkraftwerk. Aufgrund des zunehmenden Einsatzes neuer, volatiler regenerativer Energiequellen, wie Wind und Photovoltaik, ist Flexibilität bei der Netzregelung und -stabilisierung das Gebot der Stunde und daher von größtem Interesse für Energieversorger wie VERBUND. Limberg 3 wurde so konzipiert, dass es ideal auf die anspruchsvollen Anforderungen der Energiewende reagieren kann.ANDRITZ ist stolz darauf, seinen Kunden VERBUND bei der Realisierung dieses wichtigen Pumpspeicherprojekts im Herzen der österreichischen Alpen unterstützen zu können. Die Montagearbeiten vor Ort für beide Maschinen werden aktuell durchgeführt, darauf folgen diverse Inbetriebnahme-Prüfungen. Mitte 2025 sollen beide Maschineneinheiten den Vollbetrieb aufnehmen.
Erschienen in zek HYDRO, Ausgabe 5/2024